Wir haben Ihnen in unserem Blogartikel – die Top 5 Lean Methoden vorgestellt. Eine davon ist die SMED Methode, welche eine wahnsinnige Relevanz für die Optimierung von Rüstzeiten im Lean Management hat. SMED ist eine Abkürzung und steht für den englischen Ausdruck Single Minute Exchange of Die, was übersetzt so viel heißt, wie Rüsten im einstelligen Minutenbereich. Konkret werden bei dieser Methode die Umrüstzeiten an den Maschinen organisatorisch und technisch verkürzt und die Zeiten optimiert.
Was ist Rüsten und was steckt hinter dem Wort Rüstzeiten?
Rüsten ist erst einmal ein Vorgang, bei dem häufig viel manuelle Arbeit entsteht. Eine Maschine wird von Auftrag A auf Auftrag B umgebaut. Die Rüstzeit ist demnach zwischen den beiden Aufträgen, d.h. konkret die Zeit zwischen der Fertigstellung des letzten Gut-Teils von Auftrag A und der Fertigstellung des ersten Gut-Teils von Auftrag B. Gut-Teil bedeutet in diesem Falle, ein Produkt, dass keine Mängel mehr aufweist. Im Rahmen einer Kunststoffproduktion wäre das erste Gut-Teil z.B. das Produkt, das keine farblichen und qualitativen Abweichungen mehr aufweist. Gerade eine farbliche Abweichung kann in der Anlauf-Phase des neuen Produktes, in der die Maschine warmläuft, noch auftreten. Solange das Produkt also noch nicht einwandfrei ist, gehören die Ausschussprodukte zur Rüstzeit. Das Rüsten unterteilt sich in externes und internes Rüsten und teilt sich grundsätzlich in vier Schritte auf.
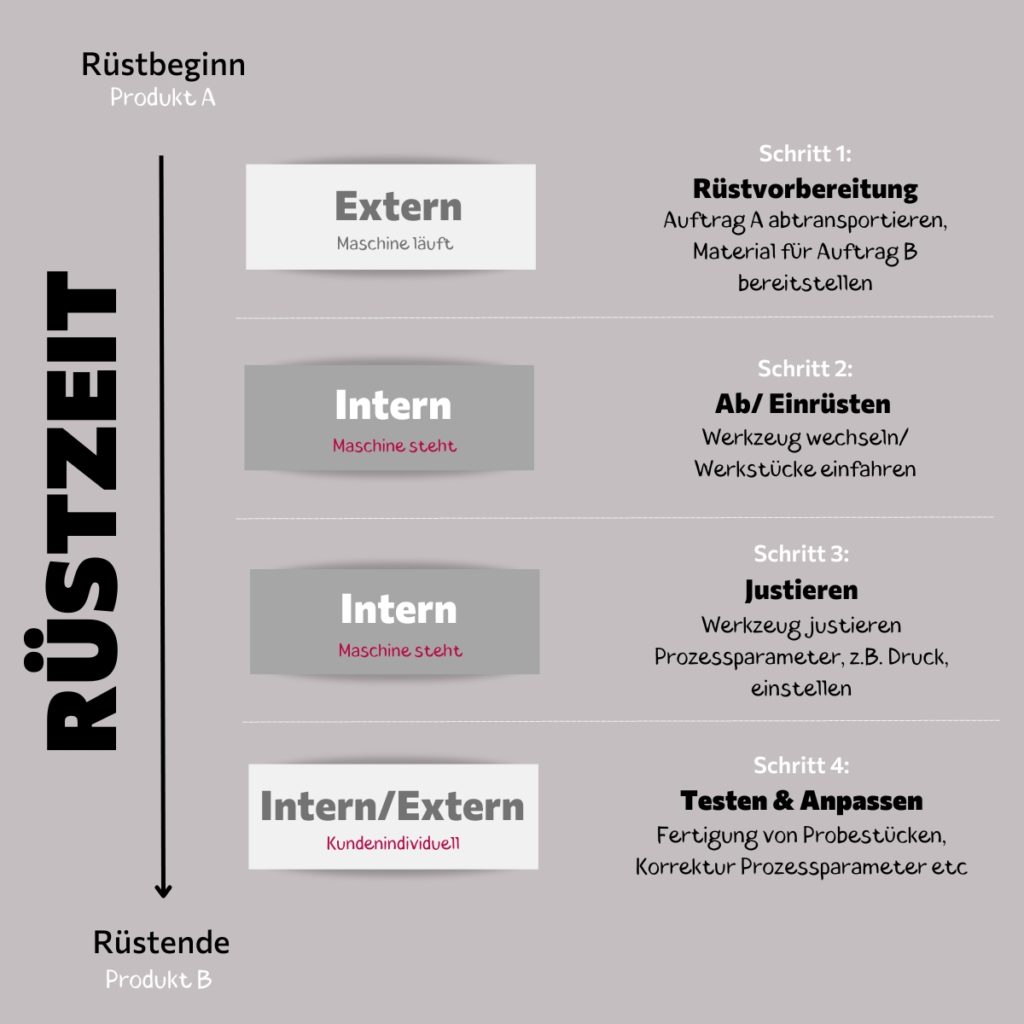
Externes Rüsten: Das sind alle Tätigkeiten, die durchgeführt werden können, während die Maschine läuft bzw. produziert. Das können Tätigkeiten, wie das Holen und Bringen von Teilen oder das Ausfüllen von Auftragspapieren sein.
Internes Rüsten: Das sind die Tätigkeiten, die nur bei stillstehender Maschine durchgeführt werden können. Zum Beispiel Werkzeug ausbauen.
Vier wesentliche Schritte eines Maschinenumbaus bzw. des Rüstens
Schritt 1: Rüstvorbereitung (i.d.R. externes Rüsten. Die Maschine läuft)
- Abtransport der gefertigten Teile aus Auftrag A
- Abmeldung des alten Auftrages A
- Anmeldung des neuen Auftrages B
- Bereitstellung aller notwendigen Materialien, Teile, Vorrichtungen, Informationen für Auftrag B.
Schritt 2: Ab- und Einrüsten (i.d.R. internes Rüsten. Die Maschine steht)
- Ausbau „alte“ Vorrichtungen/ Werkzeuge, wie z.B. Ausbau des alten Bohrers aus Auftrag A
- Montage „neue“ Vorrichtungen/ Werkzeuge, wie z.B. der Einbau des neuen Bohrers für Auftrag B
Schritt 3: Justieren (i.d.R. internes Rüsten. Die Maschine steht)
- Justieren von Vorrichtungen/ Werkzeuge
- Einstellung der Prozessparameter, wie Druck, Vorschub
Schritt 4: Testen und Anpassen (Oftmals eine Mischung aus internem und externem Rüsten)
- Fertigung von Probestücken
- Ergebnismessung und -beurteilung
- Korrektur der Prozessparameter
- Ggf. erneuter Test (Korrekturschleife)
Schritt 4 ist individuell zu betrachten und hängt vom jeweiligen Unternehmen und Rüstvorgang ab. Die Maschine läuft zwar, sie kann aber nicht verlassen werden, um andere Dinge zu tun. Man muss an der Maschine bleiben und die produzierten Teile nachmessen und die Qualität kontrollieren, bis alles passt. Somit ist hier eine 100% klare Abgrenzung von internem oder externem Rüsten oft schwierig.
Ein konkretes Beispiel zur Rüstzeitoptimierung
Es müssen 500 blaue Kunststoffbälle hergestellt werden, im nächsten Auftrag sind es 50 weiße Kunststoffkästen. Zum einen muss die Farbe gewechselt werden, zum anderen das Werkzeug, um die Bälle durch die Kästen zu ersetzen. Oft müssen auch die Maschinen neu programmiert werden, bzw. ein neues Programm muss eingelesen werden. Das alles nennt man Rüsten, Umrüsten oder Maschinenumbau. In diesem Beispiel beträgt die Rüst-Zeit 60 Minuten.
Wie kann nun die Lean Management Methode SMED helfen, die Rüstzeiten zu reduzieren?
1. Nutzen Sie eine Videokamera
Zunächst schauen wir uns den Ist-Zustand an. Unsere Empfehlung an dieser Stelle: Nutzen Sie eine Videokamera und filmen Sie gemeinsam mit den Mitarbeitern*innen den Umbau der Maschine. Das heißt, Sie begleiten die Tätigkeiten der/ des Maschinenrüsters*in für die gesamten 60 Minuten, inkl. aller Laufwege, Material- und Werkzeugsuche etc.
2. Erstellen Sie ein Spaghetti-Diagramm
Ein Spaghetti-Diagramm ist nichts anderes als ein DIN A4 Blatt auf dem Sie den gesamten Laufweg der/ des Maschinenrüster*in verfolgen und aufzeichnen. Wenn möglich organisieren Sie sich einen Hallenplan, in dem die Maschinen und Regale bereits eingezeichnet sind. Falls das nicht möglich ist, skizzieren sie das Umfeld selbst, bevor sie mit der Aufzeichnung der Laufwege starten.
Die Schritte 1 und 2 erfolgen parallel während der Ist-Aufnahme. Sie haben somit ein Kamerakind, eine*n Spaghetti-Diagramm-Zeichner*in und die/ den Maschinenrüster*in.
Danach gehen Sie gemeinsam mit dem betroffenen Team in die Analyse, um zu verstehen, wo in diesem Prozess Verschwendung stattfindet. Schauen Sie sich dafür das Video an. Sie sehen direkt anhand der Sekunden und Minuten, wieviel verschwendete Zeit an den einzelnen Stellen zugrunde liegt. Danach analysieren Sie das Spaghetti-Diagramm. Sie sehen an welcher Stelle sich Tätigkeiten „knubbeln“ andere Bereiche behindert werden, oder diese den Rüstvorgang behindern. Zusätzlich sehen Sie „Ausreißerwege“, also Wege zu einem Punkt x, der sehr weit von der Maschine entfernt ist, oder ein Punkt y der vielfach angesteuert wird. Meist sind auch diese Dinge klare Punkte für Verschwendung.
Allgemein erkennen Sie durch die Kombination von Video und Spaghetti-Diagramm, ob das Material ausreichend vorhanden ist, ob es richtig angeordnet ist oder ob die Maschinen oder Vorrichtungen an der richtigen Stelle stehen und somit die Laufwege optimal sind. Die Videoanalyse zeigt auch, ob die technischen Möglichkeiten an der einen oder anderen Stelle verbessert werden können. Unter Umständen kann sogar ein*e zweite*r Mitarbeiter*in Rüst-Tätigkeiten übernehmen, um vorzuarbeiten oder parallel zu arbeiten.
Nun geht es darum, all Ihre Erkenntnisse in eine sinnvolle Reihenfolge zu bringen und den Überblick zu behalten. Um einen geeigneten Soll-Prozess aufzubauen, können Sie Ihre Erkenntnisse nach den folgenden Schritten strukturieren.
- Eliminieren: Trennen Sie sich von Überflüssigem. Wo haben wir lange gesucht? Wo sind lange Wege?
- Kombinieren: Legen Sie Tätigkeiten zusammen, z.B. Material und Werkzeug in einem Arbeitsgang holen.
- Umverteilen: Verteilen Sie Aufgaben auf eine*n weitere*n Mitarbeiter*in um, damit parallel gearbeitet werden kann.
- Vereinfachen: Am Arbeitsplatz befinden sich nur die Werkzeuge, die für diesen Umbau benötigt werden, sie sind ergonomisch angeordnet und vielleicht sogar in der richtigen Arbeitsreihenfolge.
Durch den Einsatz der SMED Methode und die damit verbundenen schnelleren Rüst- und Umrüstzeiten reduzieren Sie Ihre Kosten. Sie können Folgeaufträge früher annehmen und haben mehr Zeit für die Produktion. Sie können Termine einhalten und gewinnen Kapazitäten.
Die SMED Methode kann aber auch anders eingesetzt werden, indem Sie diese vom klassischen Maschinenumbau auf andere Bereiche übertragen. Nutzen Sie SMED. um Prozesse an Handarbeits-, Verpackungs- oder Montagearbeitsplätzen zu verbessern. Die Handarbeitsplätze werden mit Hilfe der SMED Schritte bewertet. Auch hier gibt die Methode Klarheit zu unterschiedlichsten Formen der Verschwendung und anschließender Optimierung: Ist das benötigte Material vorhanden? Wo muss man sich auf die Zehenspitzen stellen? Wo muss sich jemand häufig bücken? Wo fehlt Material, weil es einfach nicht für den ganzen Tag reicht? SMED lässt sich also leicht auf andere Branchen übertragen und spart wirklich viel Zeit.
Praxistipps zur optimalen Anwendung der SMED Methode um Rüstzeiten zu optimieren
- Nehmen Sie eine Videokamera und filmen Sie den Umbau der Maschine. Die Aufzeichnung mit der Videokamera zeigt, welche Werkzeuge verwendet werden, ob diese gesucht werden müssen oder bereits sinnvoll und zentral angeordnet sind, welche Handgriffe ggf. doppelt ausgeführt werden etc.
- Kombinieren Sie dies mit einem Spaghetti-Diagramm. Dazu braucht man ein Stück Papier und einen Stift. Auf dem Papier ist der Grundriss des Raumes und die Position der Maschine eingezeichnet. Mit dem Stift wird der Weg des Maschinenrüsters*in notiert/gemalt. Eine Person läuft wie ein Schatten hinter dem Maschinenrüster her und zeichnet seinen Weg während des Maschinenumbaus auf. Am Ende sieht das Ergebnis wie eine sehr lange Spaghetti aus. Die andere Person mit der Videokamera läuft ebenfalls hinter dem Maschinenrüster her und achtet besonders auf die Handgriffe. Das Ergebnis der Ist-Analyse ist eine große Klarheit über die Laufwege und Handgriffe des Rüsters*in. Es wird deutlich, an welcher Stelle die Laufwege „knubbeln“. Außerdem wird deutlich, in welche Ecke der Maschinenrüster sehr häufig laufen muss und auch in welche entlegenen Ecken er sich während des Rüstvorgangs begeben muss.
- Sprechen Sie sich vor Start der SMED Analyse mit den betroffenen Personen ab und kommunizieren Sie offen und transparent im Team, dass die Ist-Analyse mit Hilfe von Videoaufnahmen nicht dazu dient, die Mitarbeiter*in zu kontrollieren, sondern dass Sie wissen wollen, welche Tätigkeiten im Prozess ablaufen. Machen Sie klar, dass der Prozess aktuell noch schlecht ist, indem die Mitarbeiter*innen arbeiten müssen.
- Bringen Sie alle Erkenntnisse nach den oben aufgeführten EKUV Schritten in eine sinnvolle Reihenfolge. Dies ist eine super Grundlage für den Aufbau Ihres Soll-Prozesses.
- Versuchen Sie von Anfang an zu lernen, indem Sie sich nach vier bis sechs Wochen im Review anschauen, was passiert ist. Nehmen Sie die Ideen aus dem Review aktiv mit in den nächsten Optimierungsprozess.
Ihre Kathrin Wortmann und Ihr Lars Kinkeldey von der Freiraum Bande